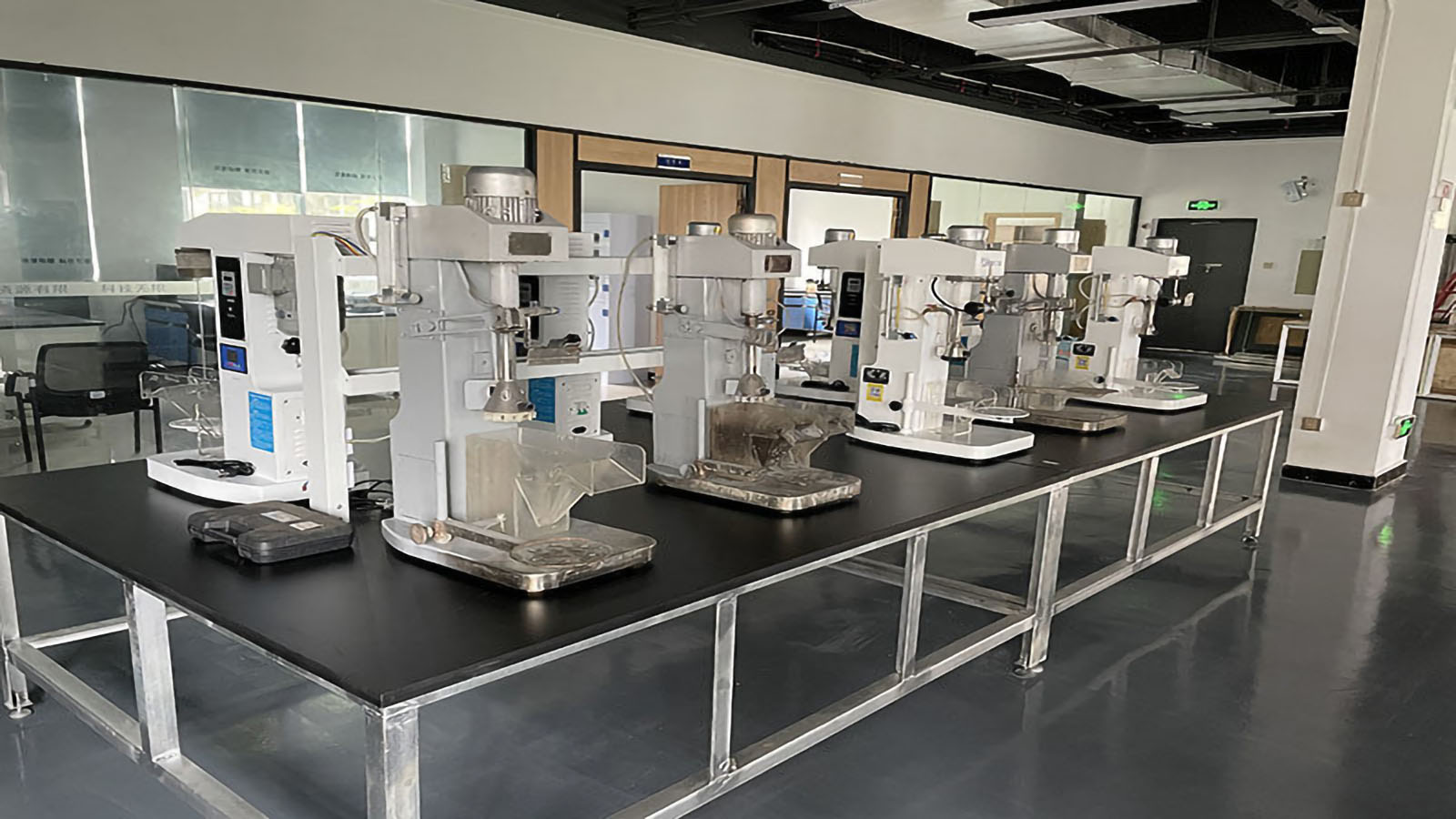
Mineral processing experiments are an indispensable part of mine development and serve as an important technical basis for mineral processing plant construction and production. Professional mineral processing experimental services can fully meet clients' needs in depth, breadth, and precision, providing scientific guarantees for the rational development of mineral resources. This article will detail the importance, process, and considerations of mineral processing experiments, helping mining investors understand how to mitigate technical risks through scientific testing.
The Importance of Mineral Processing Experiments
Some mining investors may question the necessity of mineral processing experiments, believing they can directly draw on the experience of similar mines. However, due to the different natural endowments and geographical regions of each deposit, the appropriate processes and product solutions also vary.
In fact, mineral processing experiments are the important and only way to obtain the best process flow and separation indicators for ore processing. Although mineral engineering can draw on experience from developed mines with similar ore types and plant scales, such reference is limited. Experience shows that many processing plants require immediate technical modifications right after their initial operation, primarily due to the lack of targeted experimental research during the planning stage.
Therefore, with a scientific, objective, and responsible attitude, Zexin Mining recommends processing technologies for clients based on complete experimental research and detailed comparative analysis when providing comprehensive processing plant services, ensuring the scientific validity and feasibility of the solution.
Sample Requirements for Mineral Processing Experiments
1. Experimental Sample Quantity
The amount of ore required for mineral processing experiments varies depending on the type of ore and the scale of the experiment. For laboratory-scale exploratory experiments, except for certain minerals with inherently low industrial grades, samples are usually controlled within the range of 30-50kg. Such a large sample size is needed because a conditional experiment typically requires 3-5 test points, with each point needing 500g or 1000g of sample, and a complete experimental process involves multiple conditions, thus creating a significant demand for sample quantity to complete a systematic experiment.
2. Sampling Method Recommendations
To ensure the representativeness of samples, the following points should be noted during sampling:
- Number of Sampling Points: Should be as many as possible, with no fewer than 3-5 sampling points for an industrial grade or natural type sample;
- Sampling Point Arrangement: Should be determined based on comprehensive geological research of the deposit, selecting locations that can fully represent the characteristics of the ore being studied;
- Sampling Point Distribution: Should be roughly evenly distributed throughout the orebody, not overly concentrated. There should be sampling points at both ends and in the middle along the strike of the orebody, and at the surface, shallow, and deep parts along the dip direction;
- Professional Sampling: It is recommended to hire professionals to ensure the representativeness of the samples.
Content of Mineral Processing Experiments
A systematic mineral processing experiment typically includes two major parts: ore property determination and mineral processing technology experiments:
1. Ore Property Research
- Ore spectral semi-quantitative analysis
- Multi-element analysis
- Rock and mineral identification
- Particle size screening analysis
- Ore grinding work index or grindability determination
- Ore physical property determination
2. Mineral Processing Technology Experiments
- Process scheme comparative experiments
- Condition experiments for each operation segment of the separation process
- Full-process open and closed-circuit experiments
- Mineral processing product inspection
- Reagent cost analysis
Detailed Mineral Processing Experiment Process
1. Pre-Experiment Preparation
- Data Collection: Understanding the research and production situations of identical or similar ores, as well as the future application mine conditions;
- Sample Weight Determination: Determining the sample amount needed for each experiment and the total sample amount;
- Sample Preparation: Including the preparation of material composition research samples, washing and pre-selection samples, gravity separation test samples, flotation and magnetic separation samples, etc.;
- Experimental Plan Formulation: Determining the mineral processing methods and their sequence based on ore properties.
2. Mineral Processing Stage
- Mineral Processing Method Research: Conducting multiple scheme comparative experiments based on ore properties, product quality requirements, and construction conditions;
- Separation Condition Experiments: Including flotation experiments, magnetic separation experiments, roasting-magnetic separation experiments, gravity separation experiments, electrical separation experiments, etc.;
- Product Examination: Examining grinding products, concentrate products, middling products, tailings products, classification products, etc., to understand the properties and indicators of each product.
3. Experimental Results Analysis
Scientifically processing and analyzing the original data obtained during the experiment, refining and authenticating, to form a highly accurate mineral processing experimental report that provides technical support for subsequent process design and production.
The Value of Mineral Processing Experiments
Scientific and comprehensive mineral processing experiments can provide the following value for mine development:
- Mitigating Technical Risks: Determining the most suitable process flow through experiments, avoiding large-scale retrofitting after production starts;
- Optimizing Process Parameters: Precisely determining the best parameters for each process link, improving separation efficiency;
- Improving Recovery Rates: Customizing mineral processing solutions based on ore characteristics, maximizing the recovery of valuable elements;
- Reducing Operating Costs: Optimizing reagent usage, energy consumption, and other factors through experiments, reducing production costs;
- Increasing Investment Returns: Ultimately improving the overall return on mining investments by combining all the above factors.
Conclusion
Quality experimental methods determine mineral processing success rates, and comprehensive experimental research ensures production effectiveness. Mineral processing experiments are a key link that cannot be ignored in the mine development process and are the necessary path for rational investment in mineral resource development and technical risk mitigation. Zexin Mining provides comprehensive mineral processing experimental services from sample analysis to process design, helping clients maximize the value of their mineral resources.