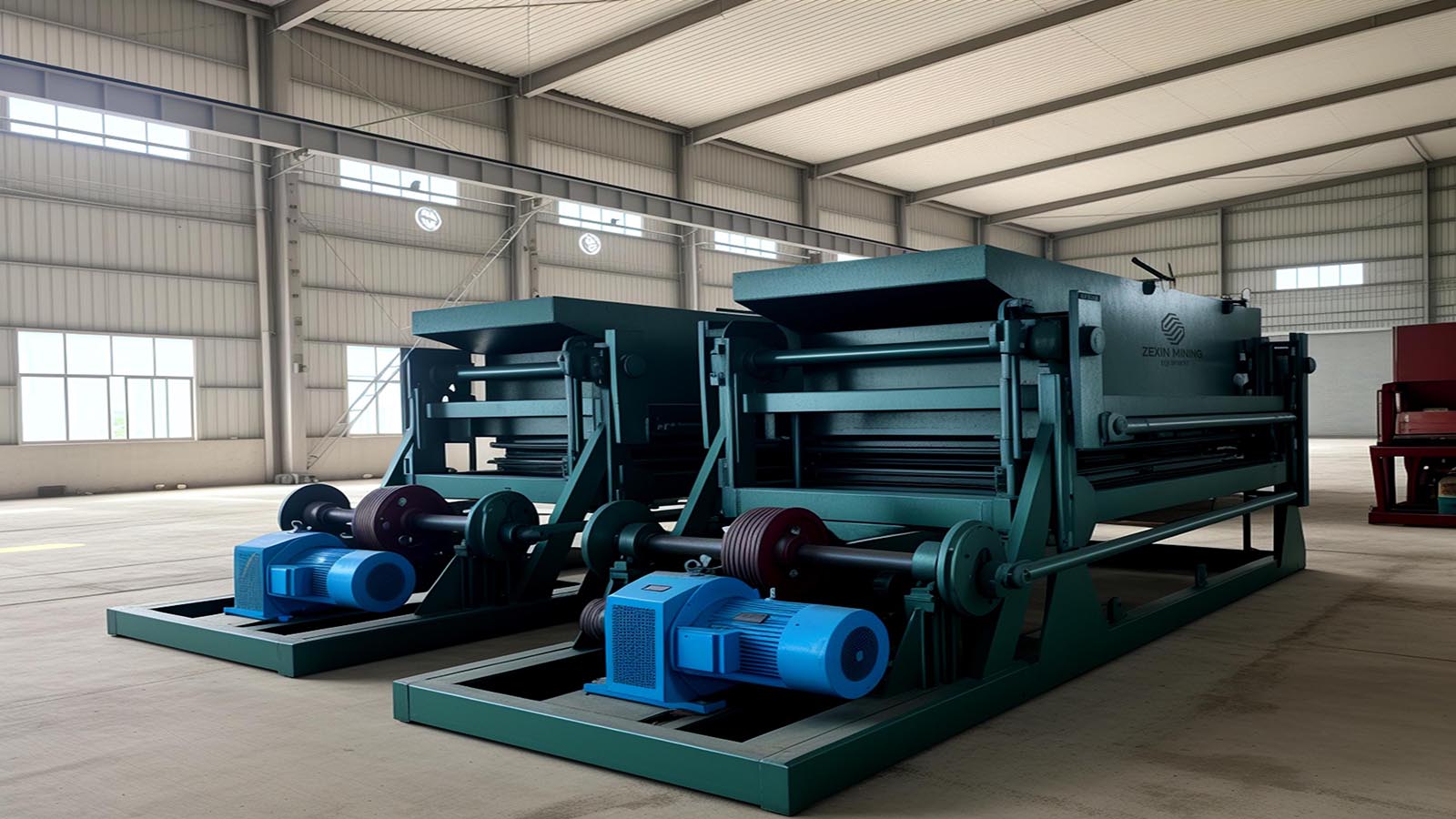
As a core equipment in gravity separation, jigging machines play a unique role in various mineral processing flows. With the decline in mineral resource grades and the increasing proportion of complex refractory ores, traditional single separation methods can no longer meet the modern mining industry's requirements for efficiency, energy conservation, and environmental protection. This article systematically analyzes the process optimization and practical applications of jigging machines in three typical ore types: complex iron ore, placer gold ore, and manganese ore, providing valuable technical references for mining enterprises.
Process Optimization of Jigging Technology in Complex Iron Ore Separation
China has a high proportion of complex iron ores containing hematite, specularite, and siderite. Due to small mineral density differences and uneven embedded particle sizes, traditional single magnetic or flotation separation methods achieve recovery rates of less than 60%, with significant concentrate grade fluctuations. Jigging technology demonstrates unique advantages in complex iron ore processing.
1. Core Functions of Jigging TechnologyIn complex iron ore separation processes, jigging machines serve two main functions:
- Coarse Particle Pre-tailing: For 0-30mm grade ore, jigging machines use vertical pulsating water flow to stratify mineral particles by density: heavy minerals (hematite, specularite) settle as concentrate, while light gangue (quartz, clay) is discharged early as tailings, reducing grinding load by over 30%
- Integrated Process Adaptability: In the "jigging-strong magnetic-flotation" process, jigging machines handle pre-concentration and tailing rejection tasks. For example, Jiugang powder ore uses jigging pre-selection before magnetic separation, increasing subsequent feed grade by 8% and metal recovery by 12 percentage points
2. Key Parameter Optimization ExperienceThrough extensive industrial practice, we have summarized key parameter optimization experiences for complex iron ore jigging processes:
- Bed Stone Particle Size Ratio: Coarse particles (35-50mm) and fine particles (25-35mm) mixed at a 1:2 ratio form an artificial bed layer with moderate porosity, balancing concentrate grade and recovery rate
- Water Flow Control: Upward water pressure of 1.5-1.7kg/cm² can maintain stable bed layer looseness, while water pressure >2.0kg/cm² causes bed layer boiling and stratification failure
- Processing Volume Control: 25-28t/h is the optimal range; too low (<19t/h) causes "empty jigging," while too high (>32t/h) increases metal loss in tailings
3. Industrial Application CaseAn iron ore processing plant implemented jigging modifications for 10-3mm rich powder ore, adjusting stroke frequency (130-350 times/min) and stroke length (27-35mm), increasing concentrate grade from 45% to 53.6%, stabilizing recovery rate at 89.5%, and reducing annual power consumption by 18%. This case fully demonstrates the significant benefits of jigging technology in complex iron ore processing.
Core Position of Jigging Machines in Placer Gold Gravity Separation
Placer gold ore separation characteristics: gold has a much higher density (15-19g/cm³) than gangue (2.6g/cm³), but challenges exist with mixed coarse and fine particles (0.1-12mm) and difficulties in recovering fine gold. Jigging machines hold a core position in placer gold gravity separation processes.
1. Core Functions of Jigging MachinesIn placer gold ore separation processes, jigging machines serve the following functions:
- Efficient Gold Capture in Roughing: Trapezoidal jigging machines utilize an expanding working surface design, with narrow inlet accelerating coarse gold particle settling and wide end extending stratification time for fine gold particles, achieving recovery rates of 85%-92% per unit
- Synergy with Shaking Tables: Jigging machines produce rough concentrate (gold content 200-500g/t) for shaking table cleaning, preventing primary ore slime from directly impacting the shaking table separation interface, improving overall process recovery to over 90%
2. Equipment Selection and Operation GuidelinesEquipment selection and operation guidelines for placer gold jigging separation include:
- Sawtooth Wave Jigging Technology: Fast upward and slow downward water flow in sawtooth wave form extends heavy mineral settling time, improving fine gold (0.1-0.5mm) recovery by 15% compared to sine wave models
- Classification Principles: 0-3mm fine sand uses JT-0.57 type jigging machines (stroke frequency 180 times/min), while 3-12mm gravel uses JT2-2 type (stroke frequency 120 times/min), avoiding particle size interference in stratification
- Water Conservation Design: Screen underflow water addition of 1-2m³/t, closed-circuit recycling system with water reuse rate >99.7%, solving the high water consumption problem in sand ore processing plants
3. Application ResultsA placer gold mine in Heilongjiang Province adopted two-stage jigging (roughing + scavenging), achieving total gold recovery of 91.5%, reducing tailings gold grade to 0.02g/t, and decreasing equipment footprint by 40% compared to traditional processes. This successful case demonstrates the excellent performance of jigging technology in placer gold processing.
Technical Breakthroughs in Coarse Manganese Ore Jigging Separation
Manganese ore resource characteristics: oxide manganese, nodular manganese with coarse embedded particles (0-30mm), but small density differences (manganese minerals 3.7g/cm³, gangue 2.6g/cm³), high flotation reagent costs, and heavy medium separation prone to muddying. Jigging technology has achieved important breakthroughs in manganese ore processing.
1. Advantages of Jigging TechnologyIn manganese ore separation processes, jigging technology offers the following advantages:
- Large Particle Size Adaptability: AM30 type jigging machines can process 30mm coarse manganese ore, using screen overflow (concentrate) and screen underflow (middlings) dual discharge routes to achieve "one-stage two-level" separation
- Enhanced Separation with Compound Valve: The main valve lifts the bed layer, while the auxiliary valve extends loosening time, improving nodular manganese liberation by 20%, achieving Mn concentrate grade of 42%
2. Key Technical InnovationsKey technical innovations in manganese ore jigging separation include:
- No-Overflow Silo-Type Discharge: Eliminating traditional overflow weirs, using variable-frequency speed-regulated discharge wheels to control bottom flow thickness, preventing large manganese ore blocks (>20mm) from mixing over weirs, reducing concentrate gangue content to <3%
- Conical Slide Valve Low-Energy Operation: Zero-clearance sealing between valve core and valve sleeve when closed, reducing energy consumption by 50% compared to plate valves, requiring only 0.2MPa air pressure for stable operation
3. Industrial PracticeA manganese ore processing plant in Guangxi Province adopted AM30+2LTC-6109/8T dual jigging machines, processing 0-30mm raw ore through two-stage separation: first-stage jigging for tailing rejection (yield 35%), second-stage jigging producing concentrate (Mn≥40%, recovery rate 88%); power consumption of only 1.8kWh per ton of ore, 40% lower than magnetic separation processes. This case fully demonstrates the technical breakthroughs and application effects of jigging technology in manganese ore processing.
Conclusion and Outlook
Jigging machines have irreplaceable roles in iron ore pre-tailing, placer gold roughing, and manganese ore classification. Zexin Mining's practical experience shows that parameter adaptation is more important than equipment selection—the same jigging machine requires high-pressure water (1.5MPa) to maintain bed layer looseness in iron ore processing, while relying on sawtooth waves to extend settling time in placer gold mining.
Future jigging technology development should focus on wide particle size compatibility and energy consumption optimization, such as the conical slide valve air system that has demonstrated energy-saving potential in manganese ore separation. With the development of automated control technology and intelligent equipment, jigging machines will play an increasingly important role in processing more complex refractory ores, providing strong support for efficient, energy-saving, and environmentally friendly utilization of mineral resources.
Related News
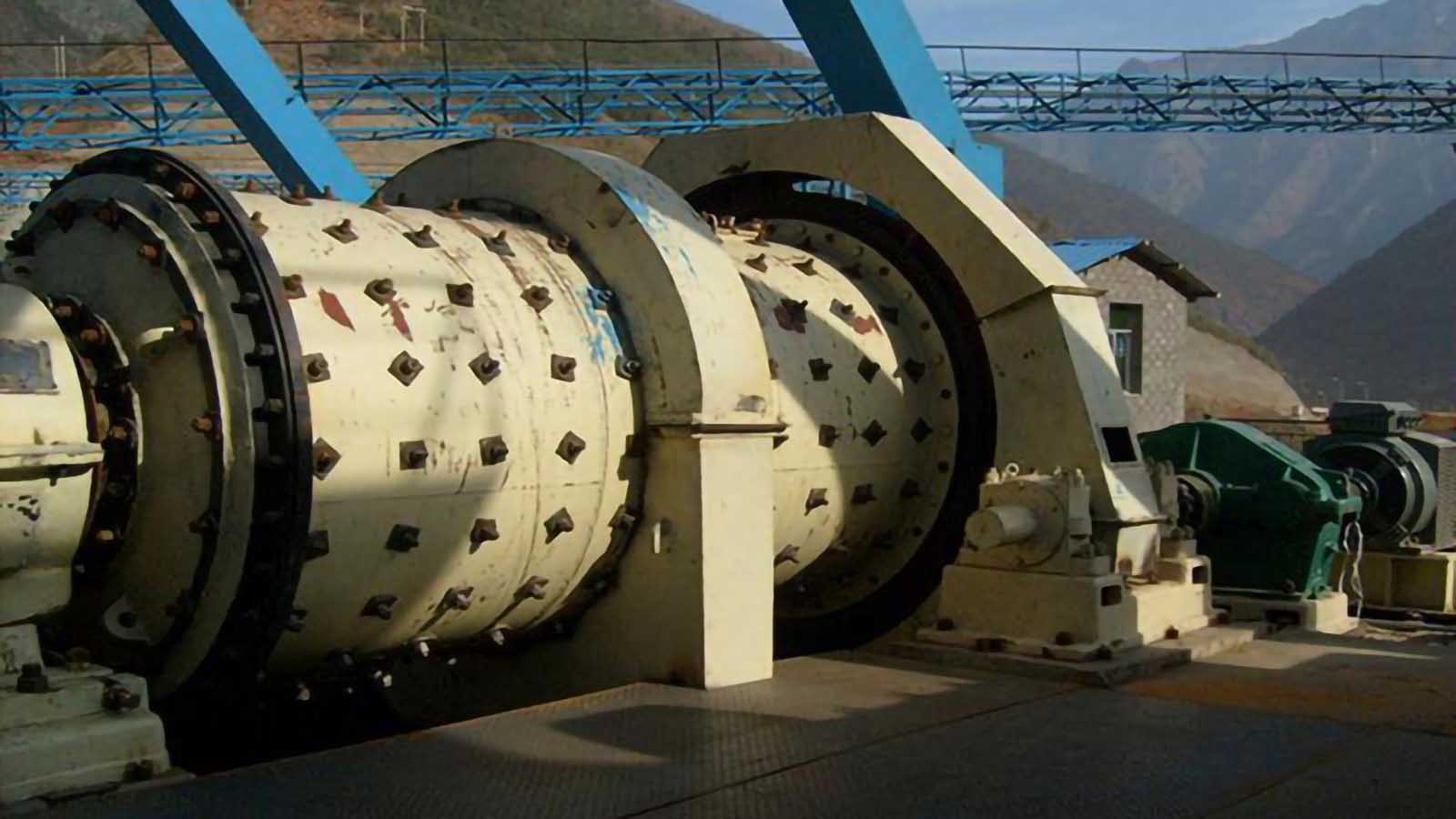
Optimizing Mineral Grinding Efficiency: The Key is Understanding Mineral 'Temperament'
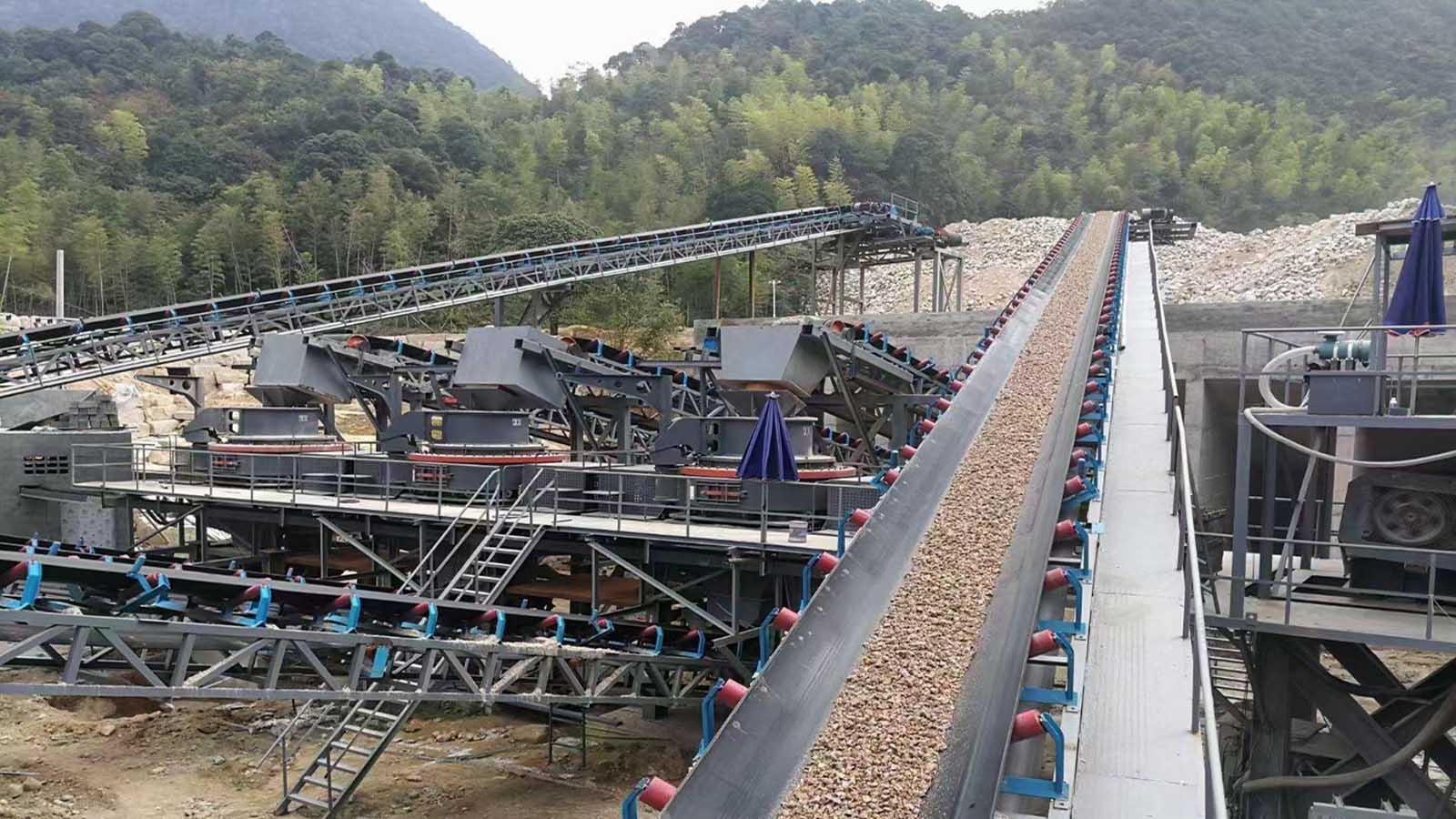
Scientific Configuration and Efficiency Enhancement of Mineral Processing Equipment: From Selection to System Integration
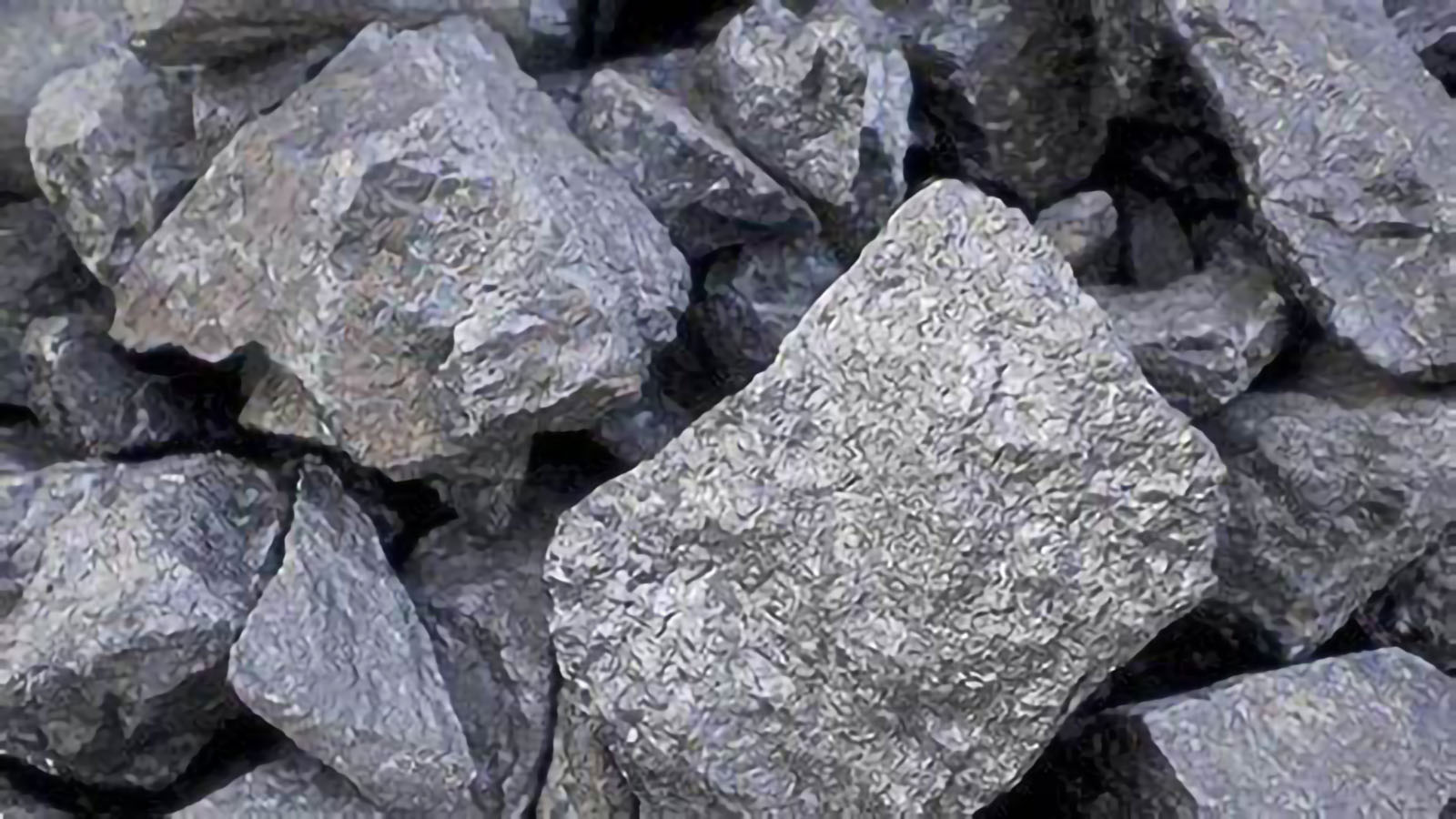