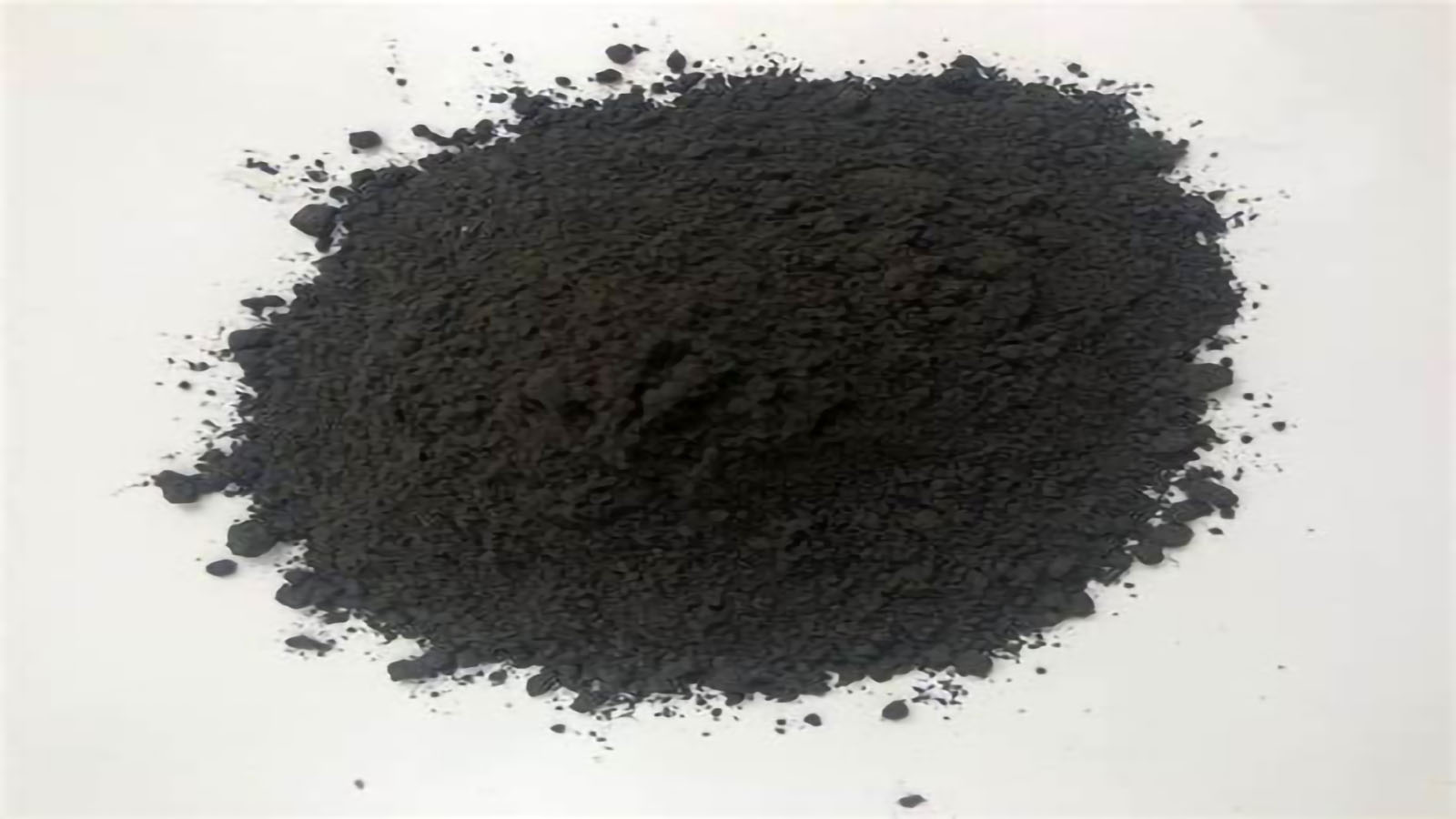
Micro-fine mineral recovery has long been a worldwide challenge in mineral processing. Through years of technical research, Zexin Mining has made breakthrough progress in this field and successfully implemented industrial applications, pioneering new approaches for efficient utilization of mineral resources.
Core Challenges in Micro-Fine Particle Separation
For micro-fine minerals (-20 microns), traditional separation efficiency drops dramatically due to mass and interface effects. The core difficulties manifest in three aspects:
1. Surface Energy DominanceThe specific surface area of mineral particles increases dramatically, leading to non-selective adsorption of reagents and a 50%-80% increase in conventional collector consumption.
2. Fluid Dynamics LimitationsBrownian motion interferes with gravitational settling, causing gravity separation equipment to stall at a recovery boundary of 20 microns.
3. Severe Gangue EntrapmentFine slimes coat the surface of target minerals, with entrapment rates exceeding 35% in -10 micron fractions of hematite-quartz mixed particle sizes.
Core Process Innovation Pathways
1. Fluidization Pretreatment Technology- Shear Flocculation Activation: Adding sodium oleate (200g/t) in high-speed agitation tanks (linear speed ≥12m/s) to induce micro-fine hematite to form 40-60 micron flocs; controlling pulp potential at Eh=+120mV~+150mV (pH=7.0) to prevent over-flocculation causing gangue entrapment; industrial practice shows recovery rates of -15 micron fraction increased from 32% to 68%
- Carrier Flotation Technology: Adding -200 mesh coarse calcite particles (carriers accounting for 20%) to adsorb micro-fine gold minerals through heterogeneous coagulation; carrier surface pre-modification using dodecylamine (100g/t) to enhance hydrophobicity; after application at a gold mine, recovery of -10 micron gold jumped from 18% to 74%
2. Composite Force Field Separation Equipment- Centrifugal Field Enhancement: Horizontal centrifugal concentrators with 80-120 times gravity acceleration (G value) enhance settling, breaking the separation limit to 5 microns; dynamic adjustment of drum inclination angle: set to 15° for cassiterite processing, adjusted to 20° for ilmenite; industrial data from a tin mine in Yunnan shows: -19 micron fraction recovery rate of 81.5%, with an enrichment ratio of 3.8
- Magnetic-Gravity Synergistic Separation: High gradient magnetic separators (background field strength 1.0T) combined with pulsating water flow (frequency 2.5Hz) to capture micro-fine weakly magnetic minerals; matrix rod optimization: peak hematite recovery rate of 88% with magnetic stainless steel wool filling rate of 60%; separation chamber backwash design: high-pressure water (0.8MPa) flushing every 30 minutes to prevent magnetic matrix clogging
3. Interface Chemistry Control Innovation- Nano-bubble Enhancement Technology: Jet vacuum generators produce 200-800nm bubbles with a number density of 10⁹ per mL; nano-bubbles enhance collision probability with hydrophobic minerals, increasing micro-fine coal flotation rate constant by 2.3 times; key controls: pulp dissolved oxygen content must be >8mg/L, pH=6.5~7.5
- Amphoteric Ion Collector Application: Sodium dodecyl aminopropionate forms double layer compression effects at pH=6.0; adsorption amount on -15 micron hematite reaches 1.8mg/m² (traditional oleic acid only 0.7mg/m²); closed-circuit flotation tests at an iron mine showed concentrate grade increased to 66.5% with SiO₂ content reduced to 3.8%
Industrial Practice and Economic Benefits
1. Anshan-type Lean Hematite Deep Recovery ProjectRaw ore characteristics: TFe 31.7%, -30 micron fraction accounting for 45%; hematite crystal size 5-15 microns, intimately associated with quartz.
Process flow:
- Stage One: High pressure grinding rolls (roller pressure 3.2kN/mm²) for selective liberation
- Stage Two: Wet high-intensity magnetic pre-concentration (background field strength 0.8T), tailings rejection rate 52%
- Stage Three: Shear flocculation (sodium oleate 250g/t, stirring speed 1200rpm)
- Stage Four: Centrifugal concentrator roughing + reverse flotation cleaning (dodecylamine/starch)
Technical indicators: Concentrate grade: 67.2% Fe; -20 micron fraction recovery rate: 76.4%; Energy consumption per ton: 11.6kWh lower than traditional processes
2. Micro-Fine Tailings Re-selection ProjectTechnical approach:
- Cyclone Classification: Φ150mm cyclones to remove -5 micron ultra-fine slimes (yield 18%)
- Efficient Thickening: Deep cone thickeners (adding APAM 15g/t) producing 65% concentration underflow
- Flotation Column Recovery: Micro-bubble generators (aperture 0.1mm) combined with hydroxamic acid collectors
Economic benefits: Recovery of 18.7% grade copper concentrate from tailings containing 0.12% Cu; Annual processing capacity of 2 million tons of tailings, creating value of 54 million yuan; Reducing tailings storage area by 35 hectares
Frontier Technology Evolution Directions
- Selective Agglomeration Technology: Microwave pretreatment (power density 4kW/kg) to activate mineral surface active sites; Precise control of hydrophobic agglomerate size at 30-50 microns, reducing gangue entrapment rate to 12%
- Intelligent Sensor-based Sorting: Terahertz wave detection of mineral lattice vibration characteristics, achieving single mineral identification at -5 microns; Microfluidic chip sorting channels (width 50μm) with processing capacity reaching 1kg/h level
- Low-carbon Biotechnology: Thiobacillus ferrooxidans selectively degrading the sulfur layer on pyrite surfaces; Biological collectors (lipopeptide types) with degradation cycles shortened to 72 hours
Micro-fine mineral recovery requires reconstructing an "interface-force field-chemistry" synergistic system: shear flocculation/carrier flotation breaks through surface energy limitations, centrifugal force field/magnetic-gravity synergy overcomes fluid dynamics bottlenecks, nano-bubbles/amphoteric reagents optimize interface behavior. Future technologies will deeply expand toward selective agglomeration, intelligent sensing, and biological extraction, pushing resource utilization rates beyond the 80% critical point.