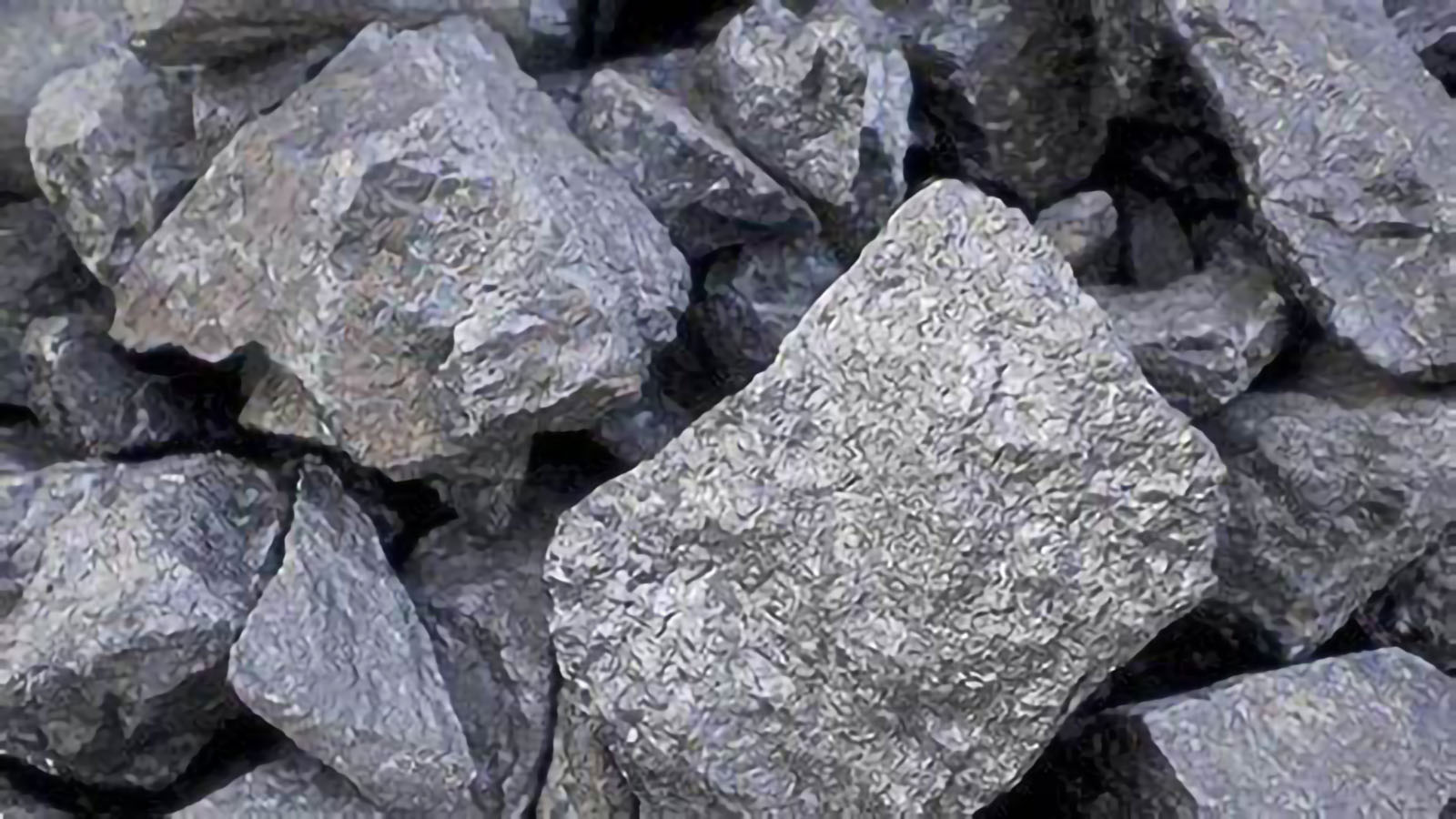
作为现代工业重要的原料矿物,锆钛矿在航空航天、电子、化工等领域具有广泛应用。随着高品质锆钛精矿需求不断增长,高效处理低品位、复杂共伴生锆钛资源已成为矿业技术领域的重大挑战。面对锆钛矿选矿中的嵌布粒度差异、表面性质相似、泥化污染严重等复杂问题,传统单一选矿方法已难以满足高品质精矿生产要求。本文系统探讨现代锆钛矿选矿工艺及其优化策略,为行业提供全面技术参考。
锆钛矿物特性与分选挑战
锆钛矿选矿技术经历了从简单的手选和重选到现代多种分选方法组合应用的演变过程。早期重选和磁选方法仅适用于处理共伴生矿物较少、锆钛矿物粒度均匀的简单矿石。这些方法在处理复杂锆钛矿时显示出明显局限性:
- 难以有效分离物理性质相近的矿物组分,如锆英砂与石英密度差仅0.5克/立方厘米
- 对微细粒嵌布矿石的选择性分离能力差,如金红石常以微细粒形态赋存于钛铁矿间隙
- 泥化污染导致选矿效率大幅下降,原矿含黏土质矿物超15%严重影响分选效果
根据我们的研究与实践,针对不同类型的锆钛矿,需采用差异化选矿工艺策略,才能最大化提升精矿品质与回收率。
预处理技术革新
有效的预处理是解决锆钛矿选矿难题的关键第一步,主要针对原矿中的泥化问题和复杂矿物组合特性开展工作:
1. 高压擦洗脱泥技术高压擦洗成为锆钛矿预处理的关键突破口:
- 高速机械擦洗:当擦洗机叶轮线速度提升至12米/秒以上时,可有效剥离矿物表面黏土膜,显著改善后续分选效果
- 多级脱泥系统:配合三级水力旋流器串联脱泥系统,能稳定脱除95%的-10微米矿泥,使后续分选作业回收率提升20个百分点
2. 矿物表面改性处理针对难以直接分选的锆钛矿物,采用特殊表面改性技术:
- 悬浮焙烧技术:在弱还原气氛(一氧化碳浓度15-18%)下对钛铁矿进行悬浮焙烧,将其磁化率提升300%,大幅降低磁选设备负荷
- 表面活化处理:使用特定调整剂选择性改变锆英砂表面性质,增强其与捕收剂的作用能力,提高浮选效率
分选工艺协同优化
锆钛矿选矿需采用多种分选方法协同作业,针对不同目标矿物选择最佳组合工艺:
1. 钛铁矿与金红石分选工艺钛铁矿回收采用强磁选-浮选联合工艺:
- 磁选预富集:采用1.2特斯拉高梯度磁选机进行预先富集,有效分离大部分钛铁矿
- 特效浮选体系:配合MOS特效捕收剂浮选,可使钛精矿品位达48%以上且回收率突破88%
- 微细粒金红石回收:对磁选尾矿中的微细粒金红石,采用阴离子捕收剂反浮选工艺,在pH值2.5-3.5的酸性条件下取得最佳效果
2. 锆英砂分选技术锆英砂分选依赖重选-电选协同工艺:
- 重选初选:螺旋溜槽和摇床串联使用,预先抛尾后富集锆英砂至30-35%品位
- 电选精选:采用20千伏高压电选机利用矿物导电性差异,成功实现-325目微细粒锆英砂回收,最终精矿品位可达65%以上
3. 独居石分离工艺稀土矿物独居石的分离需创新药剂制度:
- 酸性浮选体系:在pH值4.5的酸性环境中,使用水玻璃选择性抑制硅酸盐矿物
- 捕收剂优化:采用改性脂肪酸捕收剂优先浮选稀土矿物,精矿稀土氧化物品位可达60%
- 多级精选净化:通过3-4次精选操作,逐步去除浮选精矿中的杂质矿物,提高产品纯度
中矿资源化核心技术
中矿处理是提高锆钛矿综合回收率的关键环节,针对不同类型中矿需采用差异化处理方案:
1. 连生体中矿定制化处理连生体是锆钛矿选矿中常见的难题,需专门设计处理工艺:
- 精细磨矿技术:采用直径50毫米钢棒的棒磨机再磨,过磨率较球磨机降低40%,有效保护脆性矿物
- 分级优化:采用水力旋流器与精密筛分相结合的方式,实现窄粒级分级,提高后续分选效率
- 短流程浮选:对泥化严重的中矿实施短流程浮选,仅用三槽浮选机串联即可完成有效回收
2. 尾矿资源化利用技术尾矿资源化实现重大突破:
- 强磁扫选工艺:电选尾矿经两段强磁扫选,最终尾矿品位降至0.2%以下,实现精细回收
- 废水处理创新:选矿废水通过电催化氧化技术降解浮选药剂残留,化学需氧量去除率超95%
- 磁加载沉淀技术:采用磁性材料辅助沉淀工艺,使回水悬浮物浓度低于10毫克/升,满足循环使用要求
前沿技术发展趋势
随着技术进步,锆钛矿选矿领域正出现一系列前沿创新技术:
1. 矿物基因工程应用矿物基因工程正在改变工艺设计逻辑:
- 精准矿物解离分析:基于矿物解离分析仪的深度学习模型,可精准预测不同磨矿细度下锆钛矿物的解离行为
- 工艺优化指导:通过矿物基因图谱分析,为选矿工艺参数优化提供精确依据,指导磨矿能耗优化
- 智能流程设计:结合人工智能算法,根据矿物基因特征自动生成最优选矿流程,提高工艺设计效率
2. 智能传感分选技术新型智能分选设备在锆钛矿选矿中表现出显著优势:
- X射线透射分选:X射线透射分选机对+2毫米粗粒级原矿预抛废,显著降低30%入磨量,提高后续处理效率
- 多传感器融合技术:结合X射线、红外、光学等多种传感技术,实现对锆钛矿物的精准识别与分选
- 在线分析控制:通过在线矿浆分析仪实时监测选矿指标,自动调整工艺参数,维持最佳选别效果
3. 生态化处置新技术环保要求不断提高推动了生态化处置技术发展:
- 电芬顿深度处理:电芬顿技术深度降解有机药剂,使处理后水质满足严格环保标准
- 生物修复系统:人工湿地系统吸收重金属离子,实现尾矿库生态重建,减少环境影响
- 干式堆存技术:开发高效脱水与干排技术,将尾矿含水率降至15%以下,实现干式堆存,减少安全隐患
技术整合驱动产业升级
当代锆钛矿选矿已形成完整技术链条,各环节紧密衔接,协同发挥作用:
- 精准预处理:高压擦洗破除表面污染,改善矿物表面性质,为后续分选创造有利条件
- 窄粒级分级:实现精准分选,针对不同粒级采用差异化工艺,最大化回收率
- 多方法组合:重选、磁选、浮选、电选等多种方法有机结合,扬长避短,提高分选效率
- 中矿定制化处理:针对不同类型中矿采用专门工艺,实现吃干榨净,提高综合回收率
- 废水深度处理:通过先进工艺实现选矿废水闭环回用,减少环境影响
这套系统化技术体系使锆钛矿资源综合利用率从传统工艺的不足60%提升至85%以上。随着矿物基因数据库完善与智能分选装备普及,复杂共伴生锆钛矿资源的高效清洁利用将成为行业新常态,为锆钛产业可持续发展提供坚实技术支撑。