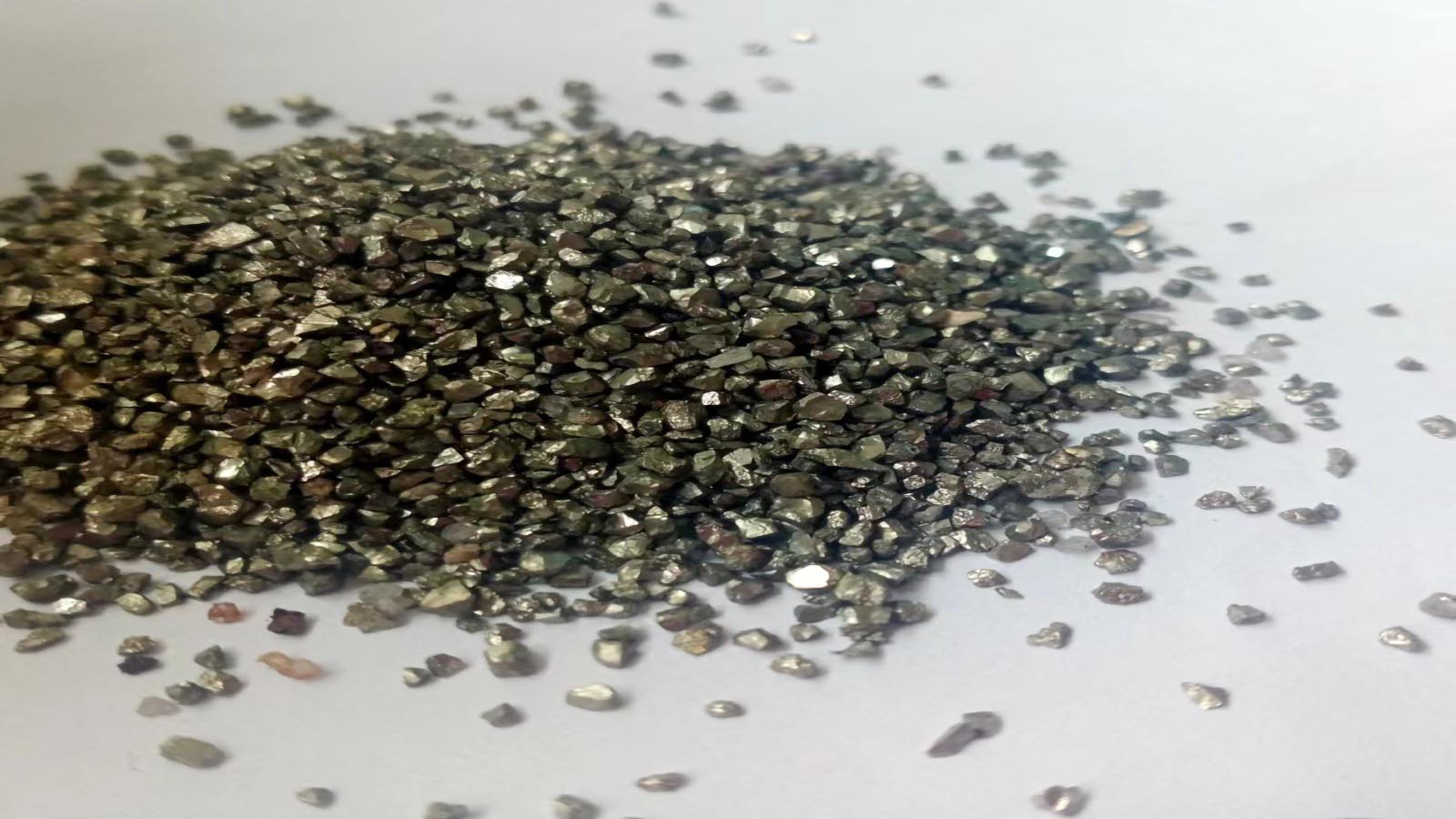
铁矿资源作为钢铁工业的基础原料,其硫含量直接影响冶炼效率和钢材质量。我国铁矿石资源禀赋复杂,约40%的矿床伴生黄铁矿、磁黄铁矿等含硫矿物,导致铁精矿硫含量普遍超标(0.3%-2.5%),不仅增加高炉脱硫负荷,更易引发钢材热脆现象。
含硫铁矿特性与脱硫难点
铁矿脱硫面临多重技术挑战,主要源于含硫矿物的复杂特性。
1. 硫赋存状态及影响铁矿中的硫主要以多种矿物形式存在:
- 黄铁矿(FeS₂):立方晶体结构,可浮性良好但易过粉碎,磨矿中生成Fe²⁺离子活化脉石
- 磁黄铁矿(Fe₁₋ₓS):存在单斜/六方两种晶型,六方晶型磁性弱(比磁化系数<25×10⁻⁶m³/kg)、可浮性差,易进入磁选精矿
- 复合硫化物:如黄铜矿(CuFeS₂)等,需兼顾硫脱除与有价金属回收
2. 工艺瓶颈选矿脱硫过程中存在三大难题:
- 嵌布粒度微细:磁黄铁矿常以5-20μm包裹于磁铁矿中,需磨至-0.045mm占90%以上方能解离
- 矿浆干扰:磁黄铁矿氧化产生的Fe²⁺消耗活化剂(如CuSO₄),导致浮选剂耗量增加30%-50%
- 分选选择性差:磁黄铁矿与磁铁矿密度重叠(4.3-4.8g/cm³),重选分离效率不足50%
脱硫主流工艺与技术突破
针对不同类型的含硫铁矿,研发了多种高效脱硫工艺。
1. 阶段磨矿—阶段选别工艺该工艺特别适用于硫矿物嵌布粒度差异显著的矿石:
- 粗磨阶段:磨至-0.074mm占65%,弱磁选(磁场强度160mT)抛除40%尾矿,同步回收粗粒硫
- 再磨阶段:磁性产品磨至-0.045mm占90%,采用反浮选脱除微细粒磁黄铁矿
安徽某铁矿采用该工艺,铁精矿品位提升至66.97%,硫含量降至0.21%,回收率保持80.3%。
2. 磁选—浮选联合工艺该工艺针对难浮磁黄铁矿开发了专门的药剂体系:
- 活化剂优化:采用稀硫酸(10%浓度)+JL-02复合活化剂,破除磁黄铁矿表面氧化膜,其接触角从35°增至78°
- 捕收剂革新:丁基黄药+Q-319组合(比例2:1),对六方磁黄铁矿吸附量提升至1.2mg/m²
内蒙古某选厂应用该工艺后,铁精矿硫含量从0.82%降至0.26%,硫回收率提高至88.69%,吨矿药剂成本降低4.3元。
3. 焙烧—磁选工艺对于难选铁矿,开发了低温高效的热处理技术:
- 技术原理:在弱还原气氛(CO浓度15%-18%)中,磁黄铁矿转化为强磁性Fe₃O₄,磁选分离效率提升至92%
- 节能突破:悬浮焙烧炉温度降至620℃(传统竖炉>850℃),燃料消耗减少35%;配套余热锅炉回收烟气热量,蒸汽发电效率达22%
关键设备与操作实践
设备创新推动了脱硫工艺效率的持续提升。
1. 浮选装备升级新型浮选设备针对含硫铁矿特性进行了专门优化:
- 充气调控系统:基于在线XRF分析仪动态调节充气量(低品位矿<1.5g/t时设定1.2m³/min·m²)
- 浅槽浮选机:深宽比0.7,配合伞形叶轮,电耗降低18%
2. 重选预抛废设备高效重选设备实现了前端预抛废:
- 跳汰机:处理30-50mm粗粒级,抛废率>40%(以攀西钒钛磁铁矿为例)
- 螺旋溜槽:DL2000型处理量达40t/h,倾斜角度45°时对-2mm赤铁矿回收率最高
3. 烟气脱硫设备创新焙烧工艺配套的气体处理设备也取得突破:
- 浸没式反应器:分割盘将气泡直径控制在0.5-1mm,气液接触面积增加300%
- 分体式设计:上筒体(含冷却模块)与下筒体(反应槽)螺栓连接,维护效率提升50%
工业实践与效益分析
各种脱硫技术在工业应用中取得了显著的经济效益。
1. 攀钢旋转喷镁脱硫技术针对特殊矿种的冶炼脱硫技术:
- 旋转喷枪:转速200rpm,镁粉分散度提升80%
- 定向调渣技术:添加CaO-Al₂O₃-SiO₂熔剂,渣相粘度从3.5Pa·s降至1.2Pa·s
该技术应用后,脱硫剂利用率提高至85%,吨钢成本下降40元,年处理铁水400万吨,创效超4000万元。
2. 微细粒脱硫经济性比较不同脱硫工艺存在明显的经济性差异:
- 反浮选:投资成本中等,运营成本高(主要是药剂成本),适用于-0.045mm细粒级
- 磁选—浮选联合:投资成本高,运营成本中等,适用于-0.074mm粒级
- 焙烧—磁选:投资成本极高,运营成本低,适用于全粒级矿石
技术发展趋势
铁矿脱硫技术正向着更精准、低碳的方向发展。
- 矿物基因研究:基于MLA(矿物解离分析)建立磁黄铁矿解离模型,指导磨矿细度优化,避免过粉碎
- 生物脱硫技术:氧化亚铁硫杆菌(Acidithiobacillus ferrooxidans)在pH=1.5、35℃条件下,72小时脱硫率>80%
- 智能控制系统:结合在线粒度仪与AI算法,动态调节磨矿-浮选参数,硫品位波动率从±0.15%降至±0.05%
铁矿脱硫需遵循"矿物特性定工艺,粒度组成选设备"原则:对粗粒嵌布硫矿物,阶段磨选仍具成本优势;微细粒磁黄铁矿则依赖活化浮选与高效装备的创新耦合。未来技术突破点在于低成本解离、选择性吸附及低碳冶金的深度整合,最终实现全流程硫定向迁移与资源化。