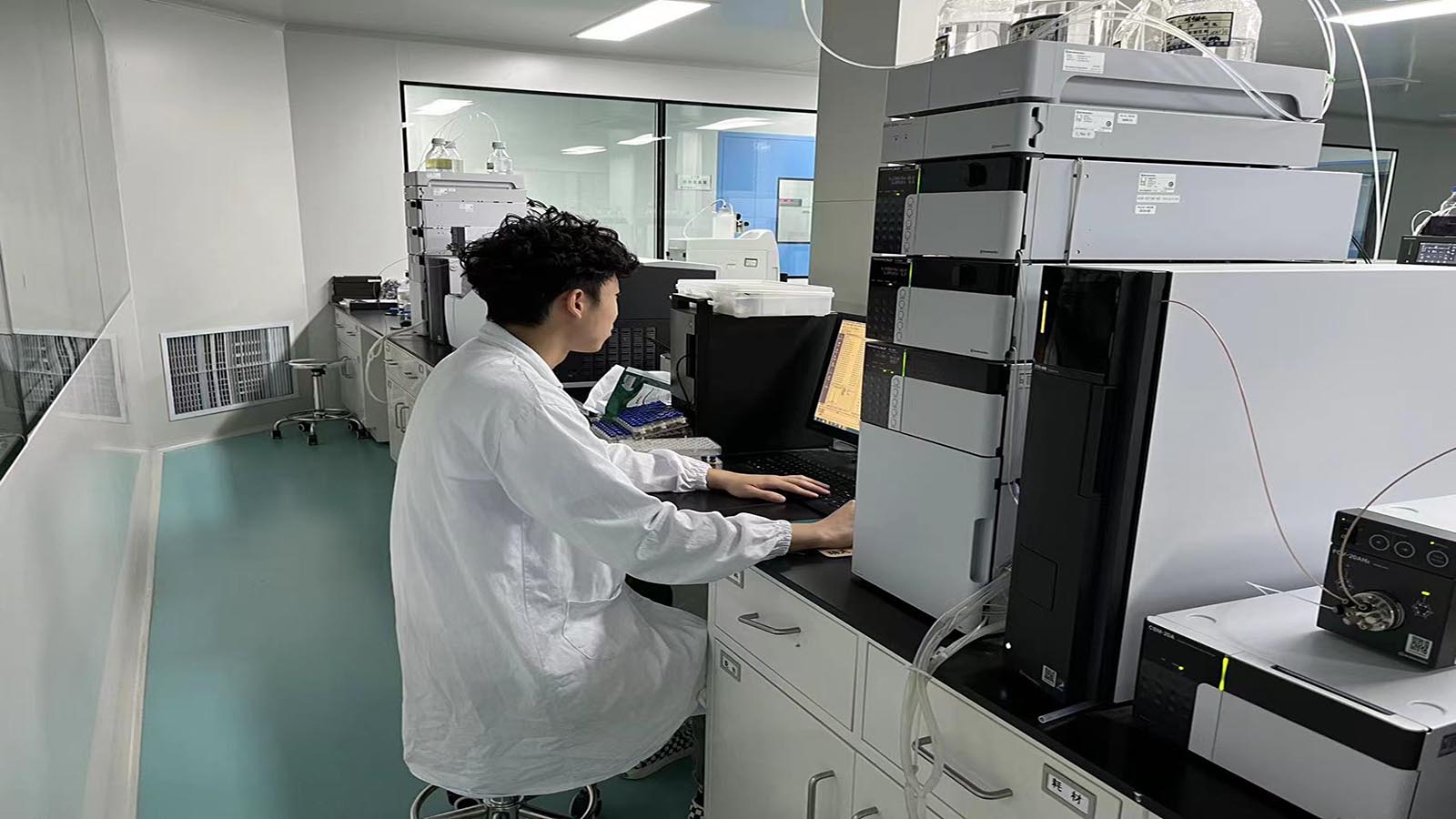
矿物嵌布粒度特征深刻决定了选矿工艺的路径选择、参数优化及最终技术经济指标。本文系统阐述了嵌布粒度实验的核心技术方法,重点分析了其在选矿工艺流程设计中的决定性作用,包括破碎磨矿流程制定、分选方法与设备选型、流程结构优化、尾矿资源化利用及经济效益评估等方面。通过具体案例分析,论证了嵌布粒度研究的不可或缺性,是选矿生产线实现高效、低耗、稳定运行的科学前提。
矿物嵌布粒度实验:内涵与方法
矿物嵌布粒度是指矿石中有用矿物颗粒的自然粒度大小及其与伴生矿物间的共生关系与空间分布特征。其核心参数包括:
- 目标矿物自身粒度分布:有用矿物颗粒的尺寸范围及其频率分布
- 嵌布关系:有用矿物与脉石矿物或其他有用矿物的接触边界性质(包裹、毗连、浸染等)
- 解离特性:在特定粉碎条件下,有用矿物单体解离的难易程度与粒度界限
核心实验技术:- 光学显微镜分析:基础手段,用于初步观察矿物组成、嵌布关系、粒度范围
- 扫描电子显微镜结合能谱分析:高分辨率观察微细粒嵌布、精确测定微区成分、分析复杂连生体
- 矿物解离分析仪:自动化定量分析大量矿物颗粒的解离度、连生体组成、粒度分布
- X射线显微CT:无损三维重构矿物颗粒及其空间分布,揭示内部包裹关系
嵌布粒度实验的核心重要性
1. 确定磨矿工艺的"靶心":目标解离粒度核心问题:有用矿物需要粉碎到多细才能实现充分的单体解离?
嵌布粒度实验作用:通过详细的矿物学研究,精确测定目标矿物充分解离所需的临界粒度。这是确定最终磨矿细度的唯一科学依据。
重要性体现:避免"欠磨"(解离不足,回收率低)或"过磨"(能耗剧增、泥化严重、分选困难、金属流失)的盲目性。过磨不仅增加吨矿电耗(占选厂总能耗的50%以上),还会恶化浮选环境,显著提高药剂消耗。
2. 指导破碎/磨矿段数与流程结构设计核心问题:需要几段破碎?几段磨矿?是采用阶段磨矿阶段选别,还是集中磨矿?
嵌布粒度实验作用:分析矿石中不同粒级范围内有用矿物的解离度和富集情况。
若粗粒级即存在较高品位的易解离矿物或富连生体,则适合采用阶段磨矿阶段选别流程,提前回收已解离或富集的粗精矿,减少后续磨矿量,降低能耗和过粉碎风险(如许多斑岩铜矿、部分金矿)。
若矿物嵌布极细且均匀,粗磨下基本无单体或富集效果差,则可能更适合集中磨矿到目标细度后再进行分选(如某些微细粒嵌布的钒钛磁铁矿、稀有金属矿)。
3. 为分选方法与设备选型提供直接依据核心问题:选用重选、磁选、浮选还是联合流程?选用何种类型和规格的分选设备?
嵌布粒度实验作用:
- 粒度范围:目标矿物的有效分选粒度范围(如重选对粗、中粒有效,浮选对细、微细粒有效)决定了主分选方法的适用性
- 解离特性与连生体性质:影响分选方法的选择。例如:若有用矿物与主要脉石密度差异显著且解离粒度较粗,重选可能是高效低耗的首选(如砂锡矿、钨矿);若矿物具有强磁性或显著磁性差异,磁选是高效手段(如磁铁矿);若矿物嵌布复杂、解离粒度细、或需要分离多种矿物,浮选更具优势
- 设备选型:分选设备的处理能力、分选粒度下限、对给矿粒度的适应性等参数,必须与目标矿物的解离粒度和分选要求相匹配
4. 优化流程结构,提高资源综合利用水平核心问题:如何设计合理的粗选、精选、扫选次数?如何处理中矿?如何回收伴生有价元素?
嵌布粒度实验作用:揭示不同粒级、不同连生体类型在分选过程中的行为差异;帮助判断中矿的性质,从而决定中矿的合理处理方式;查明伴生有价元素的赋存状态和嵌布粒度,为设计综合回收流程提供关键信息。
5. 尾矿性质评估与资源化/环保设计基础核心问题:尾矿中有价金属损失的形式?尾矿的潜在利用价值?尾矿库稳定性及环境风险?
嵌布粒度实验作用:分析尾矿中金属损失的主要原因(未解离损失、泥化损失、工艺/设备效率损失),并提供尾矿的矿物组成、粒度分布、赋存状态等信息,评估其资源化利用潜力及环境风险。
对选矿生产线设计的决定性影响
嵌布粒度实验结果是选矿生产线设计的源头性输入参数和核心决策依据,贯穿于整个设计过程:
- 工艺流程制定的"灯塔":直接决定了是采用"多碎少磨"、阶段磨选、还是单一磨选;选择重、磁、浮等主分选方法及其组合方式
- 关键设备选型与规格确定的"标尺":根据嵌布特性选择适合的破碎设备、磨矿设备和分选设备
- 工艺参数优化的"基准":设计阶段的初始工艺参数设定,必须紧密围绕实现目标矿物的有效解离和高效分选这一核心目标
- 投资估算与经济评价的"基础":工艺流程的复杂程度、主要设备的规格型号与数量、厂房规模、能耗水平等直接影响项目投资额和运营成本
- 预期技术经济指标的"预言者":基于对矿物解离难度和分选潜力的科学判断,预测设计生产线的关键技术经济指标
案例分析
1. 某大型斑岩铜矿嵌布特征:黄铜矿嵌布粒度分布宽,部分粗粒(>100μm)在较粗磨矿(如P80=150μm)下即可较好解离;同时存在大量细粒、微细粒嵌布黄铜矿。
设计应用:采用"阶段磨矿+阶段选别"流程。粗磨后(P80≈150μm)进行粗粒浮选,回收已解离和富连生的粗粒铜矿物;粗选中矿再磨至P80≈45μm后进行细粒浮选。
效益:显著降低总磨矿能耗(约20-30%),减少过粉碎,提高综合回收率。
2. 某微细粒嵌布金矿嵌布特征:金主要呈显微、次显微金包裹于黄铁矿、毒砂等硫化物中,或分散于石英等脉石中,自然金粒度极细(多数<10μm)。
设计应用:认识到常规磨矿(P80=74μm)无法实现有效解离。设计采用超细磨(P80<20μm甚至<10μm)工艺,并结合高效的微细粒浮选或浸出技术。
效益:尽管磨矿能耗高,但这是实现金有效回收的唯一途径,避免了因解离不足导致的大量金属损失。
3. 某复杂多金属矿(含铜、铅、锌、银)嵌布特征:MLA分析显示铜矿物与闪锌矿、方铅矿紧密连生,且不同矿物间可浮性差异受连生状态影响显著;银主要赋存于方铅矿中。
设计应用:基于详细的连生体分析,设计了优先浮选(部分混合浮选)+ 精矿再磨分离 + 中矿单独处理的复杂流程,优化了再磨细度和各回路浮选药剂制度。
效益:实现了多种有价金属的综合高效回收,最大限度提高了银的回收率。
结论
矿物嵌布粒度实验绝非简单的实验室分析,而是选矿工程领域一项至关重要的基础性、先导性核心研究工作。它深刻揭示了矿石加工的"天然密码":
- 它是确定"磨多细"的唯一科学标尺,直接避免能耗浪费与金属损失,奠定了选矿效率的基石
- 它是工艺流程抉择的"决策大脑",从破碎段数、磨矿方式到分选主工艺的选择,均由嵌布特征主导
- 它是设备选型与参数的"设计蓝图",确保每一台设备的能力与矿石解离需求精确匹配
- 它是资源利用最大化的"探矿灯",指导伴生元素回收与尾矿资源化路径
- 它是投资与风险的"预警系统",准确的嵌布数据是预估成本、效益及技术可行性的根本
因此,在选矿生产线设计之前,投入必要资源进行详尽、精准的矿物嵌布粒度实验研究,是确保设计流程技术先进、经济合理、生产高效、资源利用充分、环境友好的绝对前提和不可或缺的关键环节。嵌布粒度研究,是连接地质资源禀赋与高效选矿工程实践的坚实桥梁,是选矿科技由"经验"走向"精准"的核心支撑。